KENNETH A JENSEN
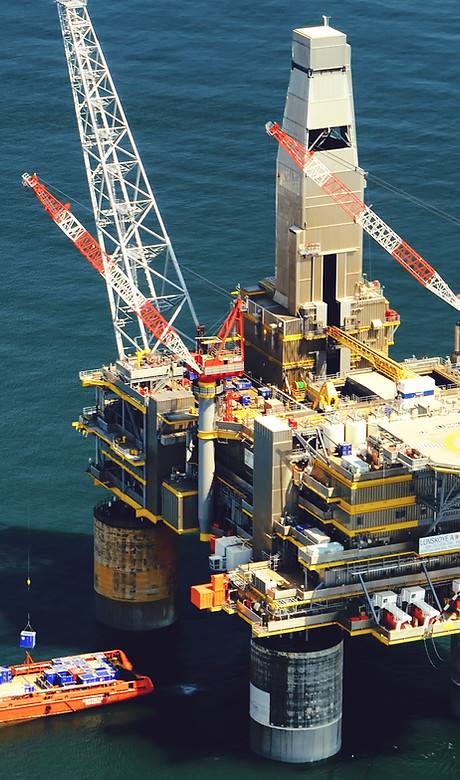
INNOVATION IN OIL AND GAS USING BIG DATA AND ANALYTICS
I was the lead data scientist during a long‑term engagement with a multinational oil and gas company as a part of an innovation team focused on the use of big data and analytics. The team was made up of highly-experienced IBM consultant with different areas of expertise and a few internal members with deep knowledge of the industry and the data architecture.
Throughout this time, my team executed a series of highly successful proof‑of‑concepts that demonstrated the specifics of how the company could utilize technology, big data, and analytics to solve individual pain points throughout their operations.
Each proof-of-concept was carefully selected based on the potential benefits, the availability of the required data, the estimated time to deliver results, and most importantly the level of innovation that would be required to produce a successful solution. Only proof-of-concepts that would lead to truly innovative solutions were considered and many of the tasks that were tackled by the team had previously been attempted in-house with little or no success.
WHEN DRILLING STRINGS GET STUCK
One of the most promising proof-of-concepts was one that delivered a series of predictive models that enabled the company to identify the occurrence of static friction events during the tripping in casing process when drilling a new well. The operations team at the rigs would be notified in real-time to minimize operational delay as static friction events are often a precursor to situations where a drilling string gets stuck in the well bore and cannot be raised, lowered, or rotated.
These events are very rare relative to the velocity of the incoming data from the drill rig - around 5 different metrics from each rig every second - and the static friction events only occur 50-100 times each day for a given rig. This is around than 0.1% of the available observations. However, when the drill string does get stuck, it is massively costly to recover from and it takes time in which the well is not producing.
The skewed data meant that I had to be creative in developing an initial screening model that could detect the records with a near-zero risk of static friction first to arrive at a better balance. I then trained a series of much more complex models to identify the static friction events from the remaining data by combining 4 different types of algorithms to reach the optimal level of accuracy.
The working proof-of-concept used a combination of IBM SPSS Modeler and IBM InfoSphere Streams to process in score the data while in-motion as well as the pushing the early warnings directly to the drill operator at the rig in real-time.
A conservative estimate computed the benefits derived from the deployment of this solution to be at least $35MM per year.
In this case, however, the infrastructure that would allow for transmitting the data from the rigs, which are often located in remote areas, to the centralized computing center and back to the rig at sufficiently high speeds was not yet in place and installing the scoring engine at each drill-site would not allow for new and improved models to be deployed over time.

OPTIMIZING THE FERMENTATION OF ETHANOL FOR BIOFUELS
The objective of another proof-of-concept was to use statistical and machine learning models to data collected from fermentation tanks at a biofuel facility during the production of ethanol. The newly developed models would replace the existing chemometric models and allow for the application of advanced analytical techniques and the inclusion of data from source other than the spectrometers that were the only source for the existing models.
The models were trained to estimate the content of different chemical components (or analytes) of a fermentation tank during the production of ethanol based on the continuous readings from the infrared spectrometers that are installed in each tank. Knowing the content of the tank in real-time allows the manufacturing process to be more efficient and produce less waste.
In a very short time, I was able to create a series of advanced models that had the same level of accuracy as or slightly better than the highly specialized chemometric models that were created using the proprietary software that was bundled with the spectrometers.
We were also tasked with designing an efficient integration of the data from the biofuel facilities and centralized data store as well as a determining a secure way to transfer the massive volume of data between the facilities and the centralized data repository.
The complete solution required the integration of several different technologies such as the spectrometer software, the company's ETL tool for data integration, IBM SPSS Modeler and R for data analysis and real-time scoring, and Aspera (now IBM Aspera) for high-speed data transfer between different sites.
The results from this proof-of-concept were taken to the next phase of realization by the company and was deployed to a production facility in a pilot program before rolling it out to the remaining facilities.

"My association with Kenneth has spanned more than 10 years and is rooted in the foundation of data mining. Kenneth and I worked together at SPSS answering some of the industry's most difficult questions.
Kenneth's skills were then superior and his ability to decompose business ambiguity was unmatched. We recently had the opportunity to develop and deploy an innovation lab for a global oil and gas corporation. Kenneth led the deep analytic function of the team and was focused on solving some very difficult problems by blending stochastic and physical models. Stochastic modeling is relatively new to petroleum engineering professionals yet Kenneth was able to bridge that gap and deliver significant results to a typically skeptical audience. His work lead specifically to process changes in the manufacturing of alternative fuels, operational changes during casing operations, and timely operational shifts in oilfield operational models.
Kenneth embodies the best qualities of a data scientist whilst being truly adaptive to the dynamic industrial environment."